At GSC we are committed to continuous improvement and technological development, a key need to maintain competitiveness in the sector.
We have a great team, great professionals with extensive experience in the machining sector, committed to the values and purpose of the company. Our staff has the latest technology at the forefront of i.4.0, backed up by constant training in automation and digitalisation.
During this last year we have been researching different technological systems adapted to our needs, in the search for improved competitiveness, these new systems have been incorporated into the production order preparation area, thus initiating the transformation towards industry 4.0. These technologies include:
– A set of rotary dispensers for the management of machining tools that allows visibility and remote management. Integrated with ERP management software to download, manage transfer orders and facilitate the organisation and control of active inventory. It also generates customised automatic transfer reports that allow us to collect a large database of information to optimise our production processes and avoid stock breakages.
– Automatic vertical warehouse with dynamic height measurement and storage for the logistics of manufacturing tools integrated with software that allows us to optimise and supervise the entire logistics process, as well as track the frequency of use of the loading units, so that the most frequently accessed units are stored in locations close to the picking bay, optimising times in the production process.
– The presetting machines for machining tools consist of fully automatic measuring cycles that reduce machine downtime by optimising set-up times, thanks to the direct presetting-machine connection that allows the assembly conditions of the machining tools to be downloaded by executing a generated programme. In addition, it allows to achieve a homogeneous quality of all our products thanks to its linear drive for a precise and fast positioning, reducing waste materials and cost of parts, increasing the safety of the manufacturing process.
– Thermal induction machine with flexible modular system that allows the semi-automatic thermal clamping of tool holders, free of errors, reducing the time in tool changes and thus optimising the machining process.
Thus pursuing automation and data exchange within the framework of manufacturing and development technologies.
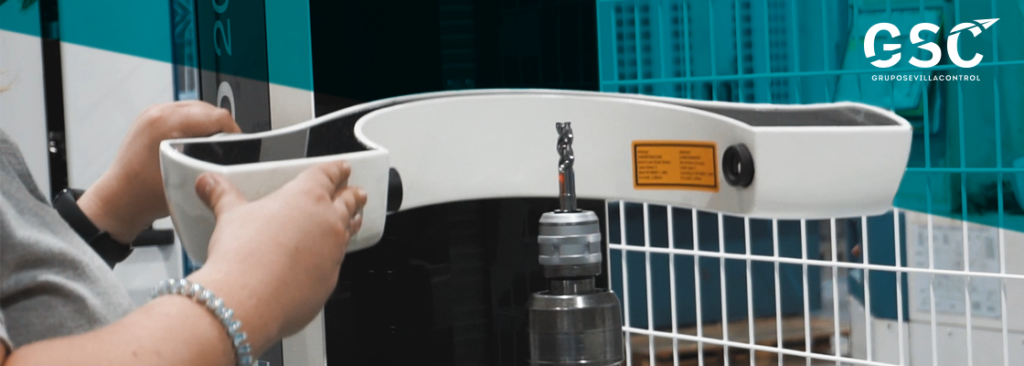